SpaceX Robotics: Inside Starship Assembly Process
Explore how advanced robotics and AI are transforming SpaceX's Starship assembly process for future interplanetary missions.
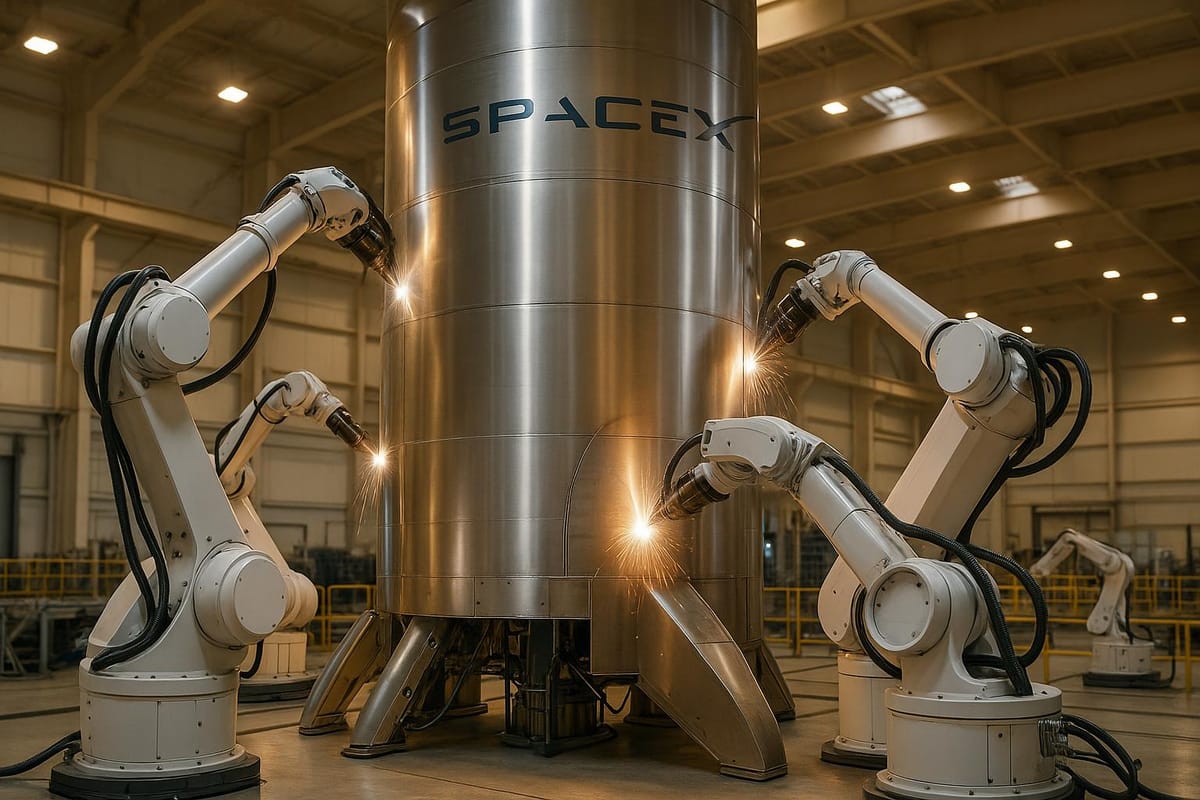
SpaceX is leveraging advanced robotics to accelerate the production of its Starship spacecraft, designed for interplanetary missions. These automated systems handle tasks like welding, assembly, and quality control with precision and efficiency. Key highlights include:
- Mechazilla Robotic Tower: Used for stacking and catching Starship stages, reducing reliance on cranes.
- Automated Engine Manufacturing: Robots produce and inspect Raptor engines 24/7 to meet high demand.
- AI Integration: Future plans include AI-driven robotics for autonomous assembly and off-Earth manufacturing.
- Production Scale: Robotics has enabled SpaceX to target producing up to 1,000 Starships annually.
First Look Inside SpaceX's Starfactory w/ Elon Musk
Key Robotic Systems in Starship Manufacturing
SpaceX relies on advanced robotics to streamline the production of Starship, handling everything from assembling massive components to crafting precision-engineered parts like engines.
Mechazilla and Launch Tower Robotics
At the heart of Starbase operations is Mechazilla, a towering system equipped with massive robotic arms - nicknamed "chopsticks." These arms are pivotal for lifting and positioning Starship sections, some of which weigh hundreds of tons. With the help of integrated sensors and control systems, these arms move with incredible precision, ensuring that even the most delicate components remain intact during the stacking process.
One of the most striking demonstrations of Mechazilla's capabilities occurred on October 13, 2024. During a test flight, SpaceX successfully caught a Super Heavy booster (Booster 12) mid-air using the launch tower's "chopsticks". Beyond catching boosters, Mechazilla also handles tasks like stacking the Starship's upper stage onto the Super Heavy booster, positioning heat shields, and integrating various components. This automation reduces the dependency on cranes and significantly lowers the risk of human error.
Automated Engine Production
When it comes to Starship's engines, SpaceX employs automated systems to keep production running 24/7. Each Super Heavy booster requires 33 Raptor engines, while the Starship upper stage uses six. Robots play a critical role in this process, performing precision welding, transferring parts, and conducting quality inspections with real-time sensor feedback. This level of automation not only meets the high production demands but also ensures the engines are built to the exacting standards required for spaceflight.
AI-Driven Robotics for Future Missions
While current robotic systems focus on production efficiency, SpaceX is looking ahead to the potential of AI-driven robotics. A major player in this vision is Tesla's Optimus robot, which leverages Tesla's AI and neural network technology - the same systems powering Tesla's self-driving cars. These humanoid robots are designed to handle repetitive or hazardous tasks. In December 2023, Tesla introduced the second generation of Optimus, showcasing improvements in motion control, hand dexterity, and energy efficiency. For instance, the Optimus V2 weighs 104 pounds, can walk at 8.05 km/h, and features 11 degrees of freedom in each hand.
Tesla has ambitious plans for Optimus production. As Elon Musk explained, "This year, we hopefully will be able to make about 5,000 Optimus robots. We're technically aiming for enough parts to make 10,000, maybe 12,000, but since it's a totally new product with a totally new, like everything is totally new, I'll say we're succeeding if we get to half of the 10,000. But even 5,000 robots, that's the size of a Roman legion, FYI".
Looking to the future, Tesla envisions mass-producing Optimus robots to assist with manufacturing tasks on Earth and, eventually, in space. These AI-powered robots could work alongside human technicians in Starship production or operate autonomously in extraterrestrial environments. Beyond Earth, they might be deployed to set up solar panels, prepare habitats, conduct surveys, or assemble equipment on Mars. This aligns perfectly with SpaceX's long-term goal of creating a self-sustaining human presence on other planets.
Starship Assembly Process and Challenges
Creating the world's most powerful rocket is no small feat. It demands a sophisticated manufacturing process that brings together thousands of components to form a highly complex spacecraft.
Step-by-Step Assembly Workflow
The assembly process at SpaceX's Starbase in Texas is driven by automation and precision. It begins with welding steel rings to construct the main sections of the Super Heavy booster and the Starship upper stage. These sections are then subjected to precision machining and thorough quality checks before advancing to the next stages.
In the structural assembly phase, robotic welding systems take over to join the cylindrical sections. For instance, the Starship upper stage, which has an empty mass of 120 tons and holds 1,250 tons of propellant, requires welds that are flawless to ensure structural integrity.
The engine integration phase is particularly demanding. Robotic systems are used to align each engine with pinpoint accuracy, guaranteeing proper connections for fuel and oxidizer flow.
Next comes the systems integration phase, where thousands of sensors, wiring harnesses, and control systems are installed. Robotic arms equipped with advanced tools navigate tight spaces within the rocket structure, performing tasks that would be too challenging or risky for human workers.
Finally, the Super Heavy booster and the Starship upper stage are brought together. Massive robotic lifting systems carefully position the upper stage onto the booster, ensuring a perfect fit for the final assembly.
Challenges in Large-Scale Assembly
Building Starship comes with its own set of challenges, largely due to the sheer size and weight of its components. Specialized tools and equipment are essential to handle these massive parts without causing damage.
Precision is critical. Every component must fit together with tolerances measured in fractions of an inch. Even the slightest misalignment could disrupt engine mounting or compromise the rocket's structural soundness.
The complexity of integrating various subsystems adds another layer of difficulty. Connections for fuel lines, electrical systems, and controls must work together seamlessly. For example, the Starship upper stage, capable of carrying a 100-ton payload, relies on thousands of components like sensors and valves to function properly.
Accessibility is another issue. Once the outer sections are assembled, reaching internal components becomes harder, complicating inspections and repairs.
On top of all this, Starship is designed to be reusable, which means every part must endure multiple flights, landings, and refurbishments. This requires higher manufacturing standards and assembly techniques to ensure durability.
Using Robotics to Overcome Challenges
To tackle these challenges, SpaceX relies heavily on advanced robotics. Custom-designed robotic arms lift and position components with extreme precision, ensuring proper alignment during integration.
Automated jigs and fixtures hold parts securely during welding and assembly, reducing the chance of human error and ensuring uniform results. Sensors embedded in these systems provide real-time feedback, enabling immediate corrections if misalignments occur.
Robotic arms with specialized tools enhance accessibility, reaching confined areas that would otherwise be difficult for human technicians to access. Automated inspection systems further improve accuracy by scanning welds, measuring tolerances, and verifying placements more effectively than manual checks.
This extensive use of robotics has revolutionized the Starship assembly process. By improving precision and reducing assembly time, these innovations not only enhance quality but also pave the way for scaling up production to meet SpaceX's ambitious plans for deep space exploration.
Efficiency and Benefits Through Robotics
SpaceX's use of advanced robotics has revolutionized the way Starship is produced, turning what was once a labor-intensive process into a highly automated and efficient operation. These robotic systems tackle production challenges by streamlining assembly, enhancing precision, minimizing errors, and improving worker safety. All of these factors play a vital role in meeting the company’s ambitious goals for interplanetary missions.
Faster Production Cycles
One of the standout advantages of robotics is the ability to work continuously without breaks, fatigue, or human limitations. Tasks that might take human welders hours - like completing a single joint - can be done by automated welding systems in a fraction of the time, all while delivering consistent quality. This constant operation accelerates production timelines and ensures SpaceX stays on track with its demanding targets. Robotic arms also excel at aligning components with pinpoint accuracy, reducing the need for rework and keeping the assembly process moving efficiently.
Improved Precision and Safety
It’s not just about speed; robotics bring a level of precision that’s hard for humans to maintain over extended periods. For instance, metalworking robots ensure parts are consistent, cutting down on time-consuming corrections. Beyond precision, these systems play a key role in worker safety. By automating repetitive and hazardous tasks, they protect employees from risks like musculoskeletal injuries or exposure to dangerous conditions. Robots can handle components in tight or risky spaces, further reducing the need for human intervention in potentially unsafe environments.
Scalability for Mass Production
Robotics also make it easier to scale up manufacturing. Unlike human workers, who require extensive training and experience, robotic systems can be quickly replicated and deployed across multiple production lines. Once an improvement is made on one line, it can be applied across others without delay, making it possible to expand production capacity efficiently. This modular approach allows SpaceX to increase output while keeping additional costs relatively low, aligning with its vision for rapid, large-scale spacecraft production.
For those curious about how SpaceX’s manufacturing innovations are impacting its growth and valuation in the private market, the SpaceX Stock Investment Guide provides detailed insights into the company’s technological advancements and their influence on its financial prospects.
Future of Robotics in SpaceX's Starship Program
Robotics already plays a key role in SpaceX's spacecraft assembly, but the company is pushing the boundaries far beyond basic automation. SpaceX’s vision for robotics includes integrating artificial intelligence, adopting modular designs, and even exploring ways to manufacture spacecraft off-Earth. These advancements are set to redefine how spacecraft are built and operated.
AI and Machine Learning Integration
SpaceX is gearing up to make artificial intelligence and machine learning central to its next generation of robotics. These systems will tackle complex assembly tasks with minimal human intervention, learning from each operation to enhance efficiency and accuracy. They’ll also predict potential failures and adjust processes in real time.
"Machine learning is a key technology that enables robots to learn from data and improve their performance over time." - NASA
Imagine robots that can analyze sensor data in real time to predict equipment issues or modify operations. For instance, if temperature changes impact welding quality, AI could tweak the process on the fly to ensure consistent results. NASA’s Perseverance and Curiosity rovers have already shown how AI can navigate tricky Martian terrain by identifying obstacles and plotting the safest routes. SpaceX aims to bring this level of adaptive intelligence to its manufacturing processes.
Modular Engineering and Automation
SpaceX is also transforming its production methods with modular automation. A prime example is the new Gigabay facility at NASA's Kennedy Space Center. This towering 380-foot structure offers an impressive 46.5 million cubic feet of processing space and 815,000 square feet of workspace. It’s designed to handle massive Starship components with its cranes capable of lifting up to 400 tons, all while housing 24 specialized work cells for integration and refurbishment.
But the modular approach doesn’t stop at facility design. SpaceX is standardizing components and interfaces so that automated systems can seamlessly replicate tasks across different production sites, including those in Texas and Florida. This scalable setup allows the company to manufacture Starships more efficiently and meet growing demand.
Robotics for Off-Earth Manufacturing
SpaceX’s boldest vision for robotics involves building spacecraft on other planets using local resources. This would drastically reduce the need to ship parts from Earth, addressing the logistical hurdles of interplanetary missions. With communication delays between Earth and Mars reaching up to 20 minutes, these robots must operate autonomously, making self-sufficient manufacturing systems essential.
Several upcoming experiments are testing these ideas. In February 2026, Caltech and Momentus Inc. will demonstrate robotic assembly in orbit using lightweight components to build a circular truss during a SpaceX Falcon 9 mission. Another experiment slated for April 2026 will explore composite-forming techniques on the International Space Station, where robots will craft hardened structures from carbon fiber and liquid monomers.
"Pushing the performers to do a demo in space means they can't just sweep challenges under the rug like they could in a lab. You better figure out how it's going to survive in the space environment." - Andrew Detor, NOM4D program manager
SpaceX’s Starship, with its reusability and ability to carry heavy payloads, is a game-changer for in-space manufacturing. It can transport large robotic systems and raw materials, enabling the construction of structures far larger and more complex than anything that can be launched from Earth. These advancements are paving the way for a future where robotics plays a central role in building humanity’s presence in space.
For those tracking how these innovations might influence SpaceX's growth, the SpaceX Stock Investment Guide provides insights into how manufacturing breakthroughs impact the company’s market value and long-term potential.
Conclusion: The Role of Robotics in SpaceX's Vision
SpaceX's robotics program serves as the driving force behind its mission to make interplanetary colonization a reality. By seamlessly integrating automation into production and operations, the company is turning its bold vision into achievable milestones.
With plans to build up to 1,000 Starships annually to facilitate Mars colonization, SpaceX relies on automation to meet these extraordinary production goals. Traditional manufacturing methods simply can't keep up with the speed and precision required. The earlier exploration of these systems highlights how robotics is central to SpaceX's long-term strategy.
Economic factors also play a significant role. Transporting materials from Earth to Mars is incredibly costly, with each kilogram of cargo requiring about 200 kilograms of propellant for launch, transfer, and landing. This cost challenge makes robotic systems capable of utilizing local Martian resources essential for building self-sustaining colonies.
SpaceX's approach to rapid iteration has been a game-changer. In 2023, the company achieved 98 successful launches, showcasing how automation supports the high-frequency operations vital for commercial space ventures. This iterative process - described by aerospace engineer Frank Norris, author of Colonizing Mars - has been key to their progress:
"Their rapid iteration model - build, test, improve, repeat - accelerates progress while minimizing risk to personnel."
Robotics is also paving the way for off-Earth manufacturing. Systems designed for tasks like robotic resource extraction are laying the groundwork for long-term settlements beyond Earth.
Looking ahead, SpaceX plans to hit 144 launches in 2024 and expand its Starlink network from around 7,000 satellites to a staggering 42,000. Robotics ties all these efforts together, from the precision needed to install heat shield tiles on Starships to the autonomous systems required for satellite deployment and deep-space missions.
For those interested in the financial side, the SpaceX Stock Investment Guide provides an in-depth look at how these advancements in automation are shaping the company's market potential and driving its growth in the space economy.
FAQs
How does SpaceX use robotics to make the Starship assembly process safer and more efficient?
SpaceX uses cutting-edge robotics to boost both safety and efficiency in the Starship assembly process. Tasks like welding and material handling, which can be risky for humans, are automated, reducing the chances of workplace injuries.
These automated systems also make production faster and more precise, ensuring that the complex assembly of spacecraft meets strict quality requirements. By combining safer working conditions with increased productivity, SpaceX can speed up Starship development without compromising on quality.
How does AI enhance SpaceX's robotic systems, and what is its potential for off-Earth manufacturing?
AI is reshaping SpaceX's robotic systems by enhancing their precision, autonomy, and efficiency. These improvements enable robots to tackle intricate tasks with minimal human input, making operations during space missions safer and more dependable. Additionally, AI equips these robots to adjust to changing conditions, making them well-suited for use in unpredictable, off-Earth environments.
Looking ahead, AI-driven robotics could revolutionize off-Earth manufacturing. Imagine robots autonomously building habitats on Mars or mining resources from asteroids. These systems could function independently in extreme conditions, significantly reducing the need for human crews. This approach has the potential to lower costs, increase scalability, and support long-term exploration and settlement efforts far beyond our planet.
How does the Mechazilla Robotic Tower improve the assembly and recovery of Starship stages?
The Mechazilla Robotic Tower has transformed how SpaceX handles the assembly and recovery of its Starship stages. Equipped with massive robotic arms, this system can catch boosters mid-air as they descend, completely removing the need for landing legs or ocean landings. This method minimizes hardware wear and tear, improves safety, and drastically cuts down the time needed to prepare for the next launch.
By simplifying these processes, Mechazilla plays a key role in advancing SpaceX's vision of a fully reusable launch system, enabling more frequent and affordable space missions.
Comments ()