How Additive Manufacturing Shapes SpaceX's Raptor Engine
Explore how additive manufacturing revolutionizes rocket engine production, enhancing speed, cost efficiency, and performance in aerospace engineering.
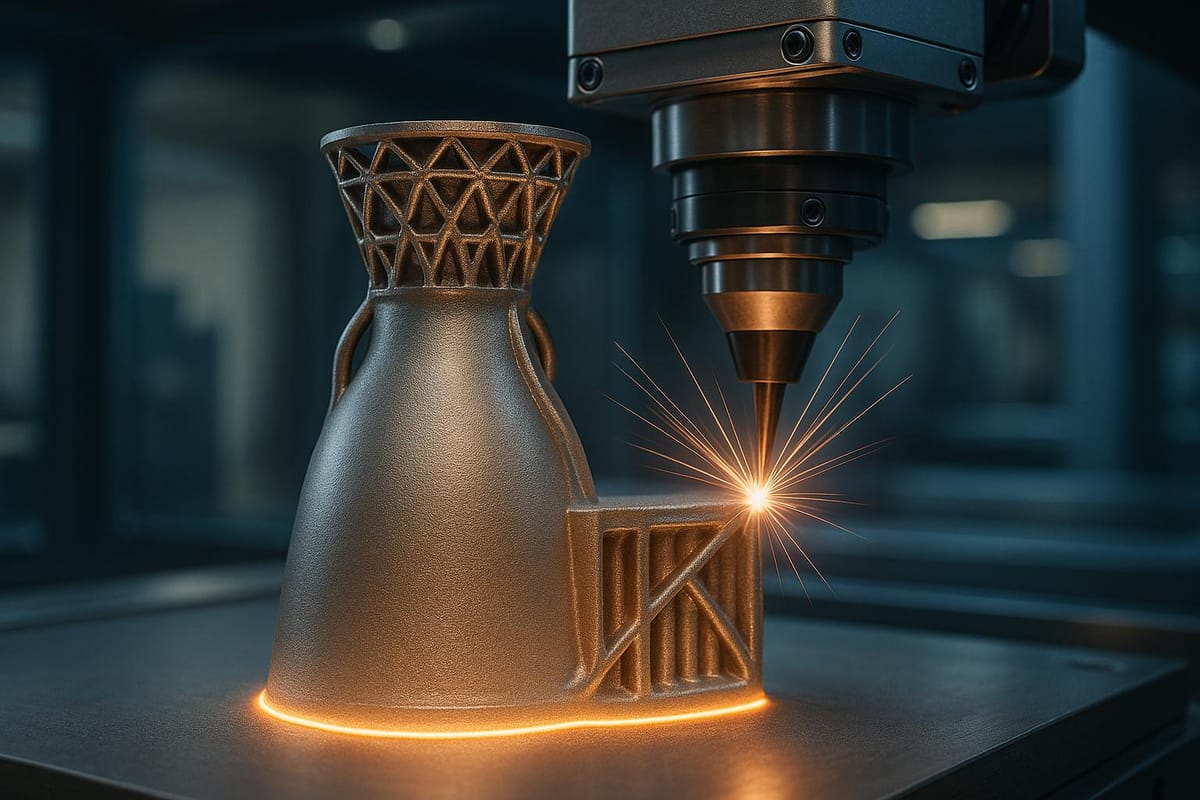
SpaceX is revolutionizing rocket engine production with additive manufacturing (AM), or 3D printing. This cutting-edge process allows SpaceX to create complex, high-performance Raptor engine components faster, cheaper, and with fewer parts compared to older manufacturing methods. Here's why AM is a game-changer for the Raptor engine:
- Faster Production: AM reduces production timelines from months to days, enabling rapid prototyping and testing.
- Reduced Costs: Consolidating multiple parts into single components lowers assembly time and minimizes potential failure points.
- Improved Performance: AM enables advanced designs, like internal cooling channels and lightweight structures, essential for handling extreme heat and pressure.
- Material Advancements: SpaceX uses specialized alloys, like GRCop-42, for durability under intense conditions.
The Genius 3D Printers That Make SpaceX Rockets
Key Engineering Challenges in Raptor Engine Development
Developing the Raptor engine pushed SpaceX engineers to rethink traditional manufacturing methods. The engine’s design posed numerous hurdles, demanding novel approaches to both engineering and production.
Managing Extreme Heat and Pressure
The Raptor engine operates in conditions that would overwhelm conventional materials. With a full-flow staged combustion cycle, it reaches chamber pressures as high as 350 bar (5,100 psi), while the Raptor 2 has achieved 330 bar during testing. These pressures generate massive thermal loads across the engine. For example, the methane pump requires 25 MW (37,550 hp), and the oxygen pump demands even more at 34 MW (45,590 hp). This level of power generates intense heat, which must be controlled through advanced cooling systems built directly into the engine’s components.
Traditional manufacturing methods simply can’t produce the intricate, continuous cooling channels needed for such systems. Every additional joint or weld increases the risk of failure, making seamless designs essential.
Designing Complex Internal Geometries
The Raptor engine’s performance depends on highly detailed internal geometries that optimize fuel flow, combustion, and cooling. Key components like the combustion chamber, injector heads, and turbopumps require precise internal structures that are nearly impossible to create using conventional manufacturing techniques. These designs are critical for managing thermal loads and ensuring efficient operation.
"SpaceX has the most advanced 3D metal printing technology in the world." – Elon Musk, Founder of SpaceX
Additive manufacturing, or 3D printing, plays a central role here. By 2016, 40% of the subscale development engine parts (by mass) were already being produced with 3D printing. This technology allows for the creation of intricate shapes, like injector heads with multiple precisely angled channels for mixing methane and liquid oxygen. Similarly, turbopumps feature curved and branching internal flow paths to enhance efficiency while keeping weight low. These integrated designs not only boost performance but also reduce the likelihood of mechanical failure.
Reducing Weight and Improving Reliability
One of the toughest challenges in rocket engine development is reducing weight without sacrificing thrust. Every pound saved on the engine translates to more payload capacity or reduced fuel requirements, but achieving this balance is far from simple.
SpaceX has made notable progress in this area. The sea-level version of the Raptor 3 weighs 3,362 lbs., compared to the Raptor 2’s 3,594 lbs.. Including vehicle commodities and hardware, the Raptor 3 totals 3,792 lbs., a dramatic reduction from the Raptor 2’s 6,338 lbs.. That’s over 2,500 pounds lighter.
"The amount of work required to simplify the Raptor engine, internalize secondary flow paths and add regenerative cooling for exposed components was staggering." – Elon Musk
This weight reduction came from simplifying the engine’s design. By consolidating multiple functions into single 3D-printed parts, SpaceX not only reduced weight but also advanced its manufacturing capabilities. A lighter engine also means smaller, lighter fuel tanks, leading to a ripple effect of weight savings throughout the rocket.
Elon Musk has described the effort as "Getting close to the limit of known physics", emphasizing the difficulty of achieving such high performance while meeting the reliability standards required for human spaceflight. These innovations highlight how SpaceX is redefining its production approach through additive manufacturing.
For those following SpaceX’s journey, these engineering feats underscore the company’s ability to tackle challenges few others can. If you're curious about SpaceX’s valuation and technological advancements, check out the SpaceX Stock Investment Guide.
Additive Manufacturing Solutions Applied to the Raptor Engine
SpaceX has redefined how rocket engines are built by using advanced additive manufacturing techniques to tackle the Raptor engine's toughest design challenges. These methods address the extreme heat, pressure, and intricate geometries required for engine performance, enabling the creation of components that traditional manufacturing simply can't achieve.
Metal 3D Printing for Engine Components
Metal additive manufacturing plays a central role in the production of SpaceX's Raptor engines. The company primarily uses Laser Beam Powder Bed Fusion (PBF-LB), a technology that enables the precise fabrication of complex components like combustion chambers and turbopumps.
To push the limits of design and performance, SpaceX combines commercially available additive manufacturing tools with custom in-house techniques. This blend of technologies gives the company unmatched control over the production process.
In September 2024, SpaceX struck an $8 million royalty-free licensing deal with Velo3D. This partnership allows SpaceX to use Sapphire printers, which are capable of producing intricate metal parts with minimal support structures, speeding up production. These advancements not only streamline manufacturing but also support the development of more integrated and efficient engine designs.
Consolidation of Engine Components
One of SpaceX's standout achievements is the ability to consolidate multiple parts into single, unified components through additive manufacturing. This approach simplifies assembly and reduces potential failure points.
"Additive manufacturing internally integrates so many formerly discrete components." – Steve Jurgenson, early VC investor in SpaceX
The Raptor 3 engine is a prime example of this strategy. By moving many external parts inside the engine, SpaceX has created a more streamlined design. Features like internalized secondary flow paths and regenerative cooling eliminate the need for separate heat shields, while the integration of plumbing and sensors enhances reliability and re-entry performance. With fewer joints, welds, and connection points, the engine becomes more robust, even under the extreme conditions of rocket operation.
Advanced Materials for Additive Manufacturing
The success of SpaceX's additive manufacturing efforts also depends on the use of cutting-edge materials. One standout is GRCop-42, a copper-based alloy designed to handle the intense heat of rocket engines. This material retains its strength under extreme thermal loads and, when paired with advanced manufacturing techniques, enables the creation of intricate cooling channels and optimized geometries that improve heat transfer.
By combining part consolidation, material innovation, and lightweight designs, SpaceX has achieved remarkable performance gains. For instance, the sea-level variant of the Raptor 3 engine delivers 21% more thrust than its predecessor, Raptor 2, while being 7% lighter.
These advancements in manufacturing give SpaceX a significant edge in the industry. For those interested in the company's technological journey and its potential impact on valuation, these innovations underscore exciting growth opportunities. To explore SpaceX's future and investment options, check out the SpaceX Stock Investment Guide.
Benefits of Additive Manufacturing for the Raptor Engine
The adoption of additive manufacturing (AM) has fundamentally changed how SpaceX develops its rocket engines, delivering quicker production, cost efficiency, and improved performance. These advancements highlight SpaceX's commitment to pushing boundaries in aerospace engineering.
Traditional vs. Additive Manufacturing: A Quick Comparison
When comparing traditional manufacturing methods to additive manufacturing, the differences are striking, especially in terms of production speed and complexity. Traditional methods often involve intricate machining, assembling thousands of parts, and time-intensive quality control, which can stretch timelines to months or even years. Additive manufacturing, on the other hand, can produce highly detailed components in just days.
Aspect | Traditional Manufacturing | Additive Manufacturing |
---|---|---|
Production Time | Months to years for complex parts | Days for intricate parts |
Part Count | Thousands of separate components (e.g., F-1 engine: 5,000+ parts) | Simplified designs with fewer parts |
Design Complexity | Restricted by machining limitations | Allows intricate geometries in a single build |
Supply Chain | Relies on multiple suppliers, leading to delays | Streamlined process with faster turnaround |
Assembly Requirements | Extensive assembly and testing | Fewer parts mean reduced assembly time |
For example, the F-1 engine from the Space Shuttle program required over 5,000 individual parts. Additive manufacturing minimizes this complexity through part consolidation, where multiple components are combined into a single piece.
Accelerated Prototyping and Testing
One of the biggest game-changers with additive manufacturing is how quickly SpaceX can prototype and test engine components. By cutting production time from months to mere days, engineers can rapidly refine designs and conduct real-time testing. This agility has been crucial for SpaceX in staying ahead of the curve.
Rocket Lab's Rutherford engine showcases this advantage, with its primary components 3D-printed in under 24 hours. Such rapid production cycles enable engineers to experiment with multiple design iterations, speeding up the development process significantly.
"Indeed. It is not widely understood that SpaceX has the most advanced 3D metal printing technology in the world." – Elon Musk, SpaceX Founder
This capability allows SpaceX to iterate and innovate at a pace that traditional manufacturing simply cannot match.
Improved Performance and Cost Efficiency
Additive manufacturing doesn't just save time - it also enhances engine performance while cutting costs. For instance, the Raptor 3 engine delivers 21% more thrust than its predecessor, Raptor 2, while being 7% lighter. These improvements stem from AM's ability to enable optimized designs, such as integrated cooling systems and consolidated parts.
By reducing the number of components, AM eliminates extra manufacturing steps and lowers the risk of part failure. Features like injectors and cooling channels, which traditionally required separate production steps, can now be integrated into a single part. This efficiency also allowed SpaceX to remove heat shields entirely from the Raptor 3 design, resulting in a lighter, simpler, and more reliable engine.
"With AM, coolant channels that would require many operations to manufacture traditionally can be designed and made in one process, e.g., part consolidation."
SpaceX's partnership with Velo3D exemplifies its dedication to advancing AM capabilities. Through an $8 million agreement, SpaceX has gained access to Sapphire printers, which can produce complex metal parts with minimal support structures, further speeding up production.
The combined benefits of fewer parts, faster production, and improved engine performance create a ripple effect. Fewer components mean fewer potential failure points, while rapid prototyping accelerates innovation. These advancements not only strengthen SpaceX's technological edge but also position the company as a leader in reducing costs and enhancing reliability. For more insights into SpaceX's progress and its potential impact on investments, check out the SpaceX Stock Investment Guide.
Impact on SpaceX's Manufacturing Strategy and Future Plans
Additive manufacturing has become a cornerstone of SpaceX's approach to building rockets and advancing space exploration. This cutting-edge technology not only enhances current production methods but also fuels SpaceX's ambitious goals. By integrating these innovations with earlier breakthroughs in engine design, SpaceX continues to strengthen its technological lead.
Supporting Reusability and Cost Reduction Goals
SpaceX's commitment to reusability gains a significant boost from additive manufacturing, which enables the creation of stronger and more efficient components. This aligns perfectly with Elon Musk's vision of making space travel more affordable.
"The revolutionary breakthrough will come with rockets that are fully and rapidly reusable. We will never conquer Mars unless we do that. It'll be too expensive. The American colonies would never have been pioneered if the ships that crossed the ocean hadn't been reusable."
– Elon Musk
Reusing rockets slashes costs by as much as 65%. For example, recovering and reusing boosters reduces manufacturing expenses by 30–50%. The Falcon 9 booster, which has been reused over 10 times with minimal maintenance, showcases the success of this approach.
Additive manufacturing plays a key role in making reusability feasible. By consolidating parts, it reduces potential failure points. Complex internal structures improve performance and lower stress, while weight reduction enhances fuel efficiency and overall rocket performance. These features are critical for ensuring the structural integrity needed for multiple launches.
The Raptor 3 SN1 engine embodies these advancements. Thanks to additive manufacturing, it features an optimized design with internalized secondary flow paths and regenerative cooling. This eliminates the need for a heat shield and fire suppression system. Additionally, the use of advanced materials bolsters durability, ensuring engines can handle multiple missions reliably.
Partnerships and Scaling Manufacturing Capabilities
SpaceX's collaboration with Velo3D has been pivotal in scaling up production. By using their advanced 3D printers, SpaceX can produce intricate metal parts such as combustion chambers and turbo pumps with minimal support structures. These printers are integral to the production of Raptor engines, and the partnership ensures SpaceX will benefit from technological improvements over the next year, with exclusive rights to adapt the technology for internal use.
This capability drastically shortens production timelines. For instance, a valve body that once took two months to manufacture can now be 3D-printed in just two days. This efficiency supports SpaceX's demanding production schedules and ambitious goals for space exploration.
Effects on the Private Space Industry
SpaceX's advancements are not just transforming its operations - they're reshaping the entire private space industry. With a valuation of $427 billion, the company's technological choices are influencing competitors like Relativity Space and ArianeGroup, who are now exploring additive manufacturing for their own rocket production.
The benefits of this technology - lighter, stronger, and more intricate components - translate into lower costs, improved efficiency, and faster production. Beyond Earth, the ability to produce complex parts on demand, even in space, could revolutionize mission planning and execution by reducing dependence on Earth-based manufacturing.
These innovations also have broader implications. The techniques SpaceX develops could eventually impact industries like automotive, aerospace, and industrial manufacturing. For investors, these advancements are more than technological achievements - they represent competitive advantages that strengthen SpaceX's market dominance. By combining cost savings, performance gains, and production speed, SpaceX creates barriers that are tough for competitors to overcome. To learn more about how these developments could influence SpaceX's market position, check out the SpaceX Stock Investment Guide.
Conclusion
Additive manufacturing has completely transformed SpaceX's approach to rocket engine development, showcasing how advanced technology can align with bold engineering ambitions. With an $8 million investment in 3D printing technology, SpaceX has achieved feats that traditional methods simply couldn’t deliver.
The Raptor 3 engine is a prime example of this transformation. It now features integrated cooling systems and internalized components, eliminating the need for bolted connections and heat shields. By using advanced materials like GRCop-42, SpaceX 3D-prints intricate parts - such as combustion chambers and turbo pumps - in single pieces, which reduces weight, minimizes failure points, and enhances reliability.
Additive manufacturing also accelerates prototyping and design iteration. SpaceX's collaboration with Velo3D's Sapphire system has been critical in handling the complex geometries required for these cutting-edge components.
These advancements not only boost engine performance but also cut costs, reinforcing SpaceX's position as a leader in affordable space exploration. Their success with additive manufacturing has set a new benchmark for innovation in aerospace.
As the industry increasingly adopts additive manufacturing, SpaceX’s work with the Raptor engine serves as a compelling example of how rocket design and production can be reimagined. For those curious about how these technical strides may influence SpaceX's long-term growth, the SpaceX Stock Investment Guide offers detailed insights into the company’s future prospects and investment potential.
FAQs
How does additive manufacturing enhance the performance and reliability of SpaceX's Raptor engine?
Additive manufacturing is a game-changer for SpaceX's Raptor engine, significantly boosting its performance and dependability. By harnessing advanced 3D printing methods, SpaceX can design complex internal cooling channels and merge multiple parts into single, seamless components. This approach cuts down the number of bolted joints, simplifies the overall design, and strengthens the engine's structure.
These advancements translate into better thermal management, greater fuel efficiency, and higher thrust. Take the Raptor 3 engine, for instance - it uses these techniques to deliver impressive thrust levels of about 2,300 to 2,500 kN while maintaining top-tier reliability. On top of that, additive manufacturing speeds up prototyping and design iterations, allowing SpaceX to fine-tune its engines more quickly and push the boundaries of rocket technology.
What makes additive manufacturing better suited for building rocket engine components compared to traditional methods?
Traditional manufacturing of rocket engine components comes with its fair share of hurdles. For starters, production can take over six months, thanks to labor-intensive processes like manually machining and sealing cooling ducts into solid materials. On top of that, these methods are expensive, waste a lot of material, and severely limit design possibilities.
Enter additive manufacturing - a game-changer for this process. With this technology, complex and integrated parts like thrust chambers can be created in just a few days. It slashes costs, cuts down on material waste, and opens the door to innovative designs that boost performance. Features like improved heat transfer and stronger structural stability are now within reach. Plus, by skipping multiple manufacturing steps, additive manufacturing achieves intricate geometries that traditional methods simply can't match.
How does SpaceX use advanced materials like GRCop-42 to improve the Raptor engine's performance in extreme conditions?
SpaceX uses GRCop-42, a copper-chromium-niobium alloy initially developed by NASA, to boost the Raptor engine's performance in extreme conditions. This material excels at dissipating heat, keeping the engine cool even during intense operations. It also holds its strength at high temperatures and resists wear, which adds to the engine's durability and efficiency.
With additive manufacturing techniques, SpaceX can precisely create intricate engine components from GRCop-42. This approach allows for designs optimized for better performance and extended lifespan, addressing the tough engineering demands of building powerful, reusable engines for space missions.
Comments ()